Practice Free MB-330 Exam Online Questions
You need to recommend a process for planned orders that will not be firmed.
What should you recommend?
- A . Change the status to Unprocessed
- B . Set the planned order to Completed
- C . Delete the planned order
- D . Change the status to Approved
- E . Remove the planned order from selection
B
Explanation:
Reference: https://docs.microsoft.com/en-us/dynamics365/supply-chain/master-planning/maintain-planned-orders
DRAG DROP
You need to configure quality controls.
Which solution objects should you configure? To answer, drag the appropriate solution objects to the correct configurations. Each solution object may be used once, more than once, or not at all. You may need to drag the split bar between panes or scroll to view content. NOTE: Each correct selection is worth one point.
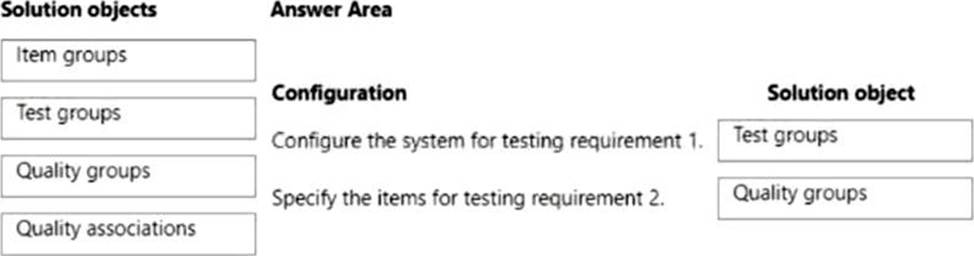
Explanation:
Box 1: Test groups
Requirement 1: 100 percent of all nutritional supplements and 50 percent of all energy drinks must be tested when production orders are completed. After a product is in testing, 100 percent of all tests must be completed.
You use the Test groups page to set up, edit, and view test groups and the individual tests that are assigned to them. The upper part of the page shows the test groups, and the lower part shows the tests that are assigned to a selected test group.
You assign several policies to a test group, such as a sampling plan, an acceptable quality level (AQL), and the requirement for destructive testing. Then, when you assign an individual test to a test group, you define additional information, such as the sequence, documents, and validity dates. For a quantitative test, the information that you define also includes the acceptable measurement values. For a qualitative test, the information includes the test variable and default outcome.
The test group that is assigned to a quality order defines the default set of tests that must be performed on the specified item. However, you can add, delete, or change tests for the quality order. Test results are reported for each test on a quality order.
Box 2: Quality groups
Requirement 2: 75 percent of all nutritional supplements and energy drinks should be tested against their required tests during an outbound process.
Quality groups
A quality group represents common testing requirements for items.
Use and create item quality groups to logically group products so that they can be assigned to quality associations for the automatic generation of quality orders.
Example of an item quality group
A manufacturing company purchases various raw materials that have the same testing requirements for incoming inspection. Therefore, the company defines a quality group and then assigns the item numbers that are associated with the raw materials to that group. Later, the company purchases a new type of raw material that has the same testing requirements. Instead of setting up new testing requirements for the new material, the company adds the item number for the new material to the existing quality group.
Reference:
https://docs.microsoft.com/en-us/dynamics365/supply-chain/inventory/quality-management-processes
https://docs.microsoft.com/en-us/dynamics365/supply-chain/inventory/quality-groups
https://docs.microsoft.com/en-us/dynamics365/supply-chain/inventory/quality-test-groups
DRAG DROP
A company opens a new warehouse facility.
You need to receive items on a transfer order by using an arrival overview.
In which order should you perform the actions? To answer, move all actions from the list of actions to the answer area and arrange them in the correct order.
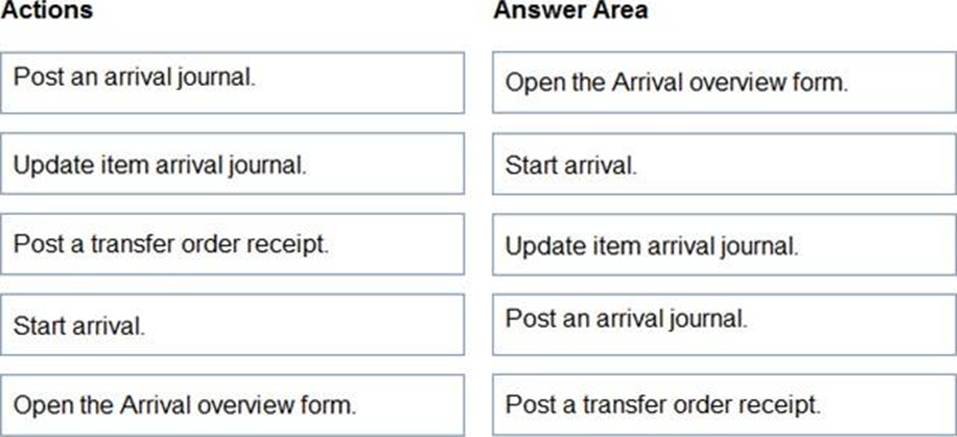
Explanation:
Reference: https://docs.microsoft.com/en-us/dynamics365/supply-chain/inventory/arrival-overview
A buyer reviews the orders generated by Planning Optimization. The buyer observes that the output for some orders appears incorrect.
The buyer reviews the history and planning logs.
Which two types of information are in the history and planning logs? Each correct answer presents part of the solution. Select all answers that apply.
- A . list of planned orders created
- B . start time a job was run and the status
- C . additional information and warnings
- D . end time a job stopped and the status
- E . list of planned orders with firm history
B, C
Explanation:
https://docs.microsoft.com/en-us/learn/modules/work-costing-sheet-dyn365-supply-chain-mgmt/
https://docs.microsoft.com/en-us/learn/modules/planning-optimization/
DRAG DROP
A company uses Dynamics 365 Supply Chain Management to sell automobile tires.
The company sells different models of tires. Each model is available in different diameter sizes. The combination of a model and its diameter represents an individual stock keeping unit (SKU).
The manufacturer’s suggested retail price (MSRP) and purchase prices can vary between variants.
The purchase price for the variants will change over time, but the MSRP will never change once it is configured. All price changes must be documented systematically. The MSRP must be the default selling price for the item if no other pricing is available.
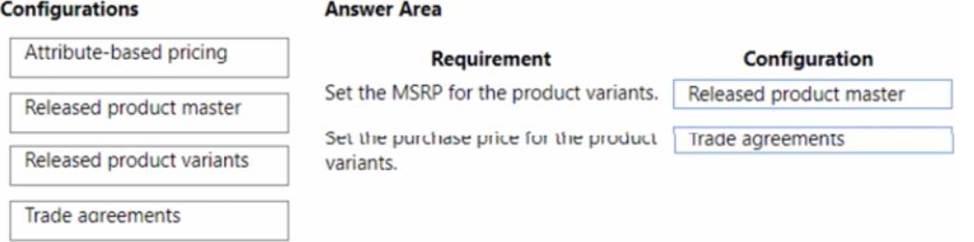
You are the warehouse manager at a distribution center.
In the warehouse, items must be moved to a staging location before moving to the baydoor location for shipping.
You need to set up a work template that accomplishes this pick/put scenario.
Which two actions should you perform? Each correct answer presents part of the solution. NOTE: Each correct selection is worth one point.
- A . Create one work class ID with valid location types of staging and baydoor. Assign these to the work template details.
- B . Create two work templates: one is a pick/put from inventory to staging and the other is from staging to baydoor.
- C . Create a sales order work template with two pick/put pairs: one to staging and the second to baydoor.
- D . Create two work class IDs: one with valid put location types of staging and the other of baydoor. Assign these to the appropriate put work types on the work template.
BD
Explanation:
Reference: https://docs.microsoft.com/en-us/dynamics365/supply-chain/warehousing/control-warehouse-locationdirectives
A distribution company uses Dynamics 365 Supply Chain Management.
The company implements a new safety policy. The policy dictates that all business units must undergo a rapid routine safety checkup every week
To follow the new policy, the warehouse manager must ensure the following:
• The business unit must be unavailable for use during that period.
• The maintenance activities must be conducted during the lunch break to avoid production downtime losses.
You must configure the system to meet the safety requirements.
Which two configurations should you complete? Each correct answer presents a part of the solution. NOTE: Each correct selection is worth one point.
- A . Work order service levels
- B . Asset BOMs
- C . Attributes
DRAG DROP
A client uses Dynamics 365 Supply Chain Management.
You need to configure automatic freight reconciliation.
Which configuration options should you use? To answer, drag the appropriate configuration options to the correct requirements. Each configuration option may be used once, more than once, or not at all. You may need to drag the split bar between panes or scroll to view content. NOTE: Each correct selection is worth one point.
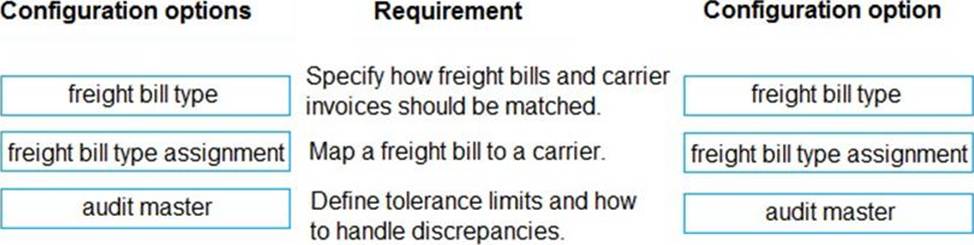
Explanation:
Reference: https://docs.microsoft.com/en-us/dynamics365/supply-chain/transportation/tasks/set-up-automatic-freight-reconciliation
DRAG DROP
You need to determine Operator1s next steps.
Which next two process steps should Operator1 complete? To answer, move the appropriate processes to the correct process steps. You may use each process once, more than once, or not at all. You may need to drag the split bar between panes or scroll to view content. NOTE: Each correct selection is worth one point.
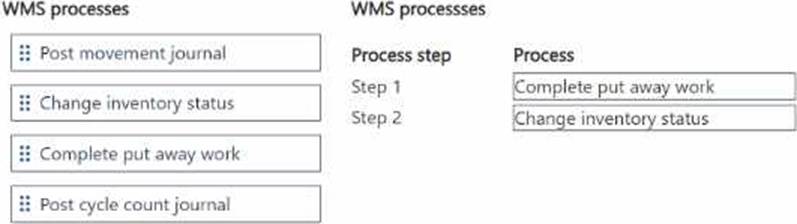
You need to configure the structure for the new line of perfumes.
What should you do first?
- A . Create a procurement category hierarchy.
- B . Create a new product with racking dimensions.
- C . Create a new product with storage dimensions.
- D . Create product configurations.
- E . Set up a new product master and implement serial tracking.